- TEAM
MMSMC
ROBBINS
- SERVICES
TBM’s Tunnel Boring Machines
- CATEGORY
TBM’s Machines
Nepal has been digging tunnels using the conventional drill and blast since 1950s. The D&B method is a standard method to dig tunnels not only in Nepal but worldwide. However, in the recent past the use of mechanized tunneling methods using Tunnel Boring Machine (TBMs) are becoming increasingly popular methods to dig tunnels of longer lengths. Nepal used its first TBM in 2015 to dig the tunnel for Bheri Babai Diversion Multipurpose Project. The TBM manufactured by Robbins-A global TBM Company and supplied through MMSM to the contractor appointed by Department of irrigation (DoI), Nepal was successful in completing the tunnel boring of 12.3 KMs of tunnel in just 17 months. This could have taken more than 10 years if dug through Drill & Blast method.
Similarly, the second TBM project in Nepal Sunkoshi Marine Diversion Multipurpose Project under the same department opted to dig its 13.3 KM tunnel using the TBM manufactured and redesigned by Robbins. The tunnel was completed in 19 months about 7 months ahead of schedule.
These successes have proven the worth of TBM’s in Nepal. Now more and more contractors and Developers are exploring the option of using TBMs for their tunnels. The initial capital investment in this method creates a doubt among the tunneler, however it has been seen globally and in Nepal that the significant time saved by using the machine, completely justifies the initial investment. Any tunnels longer than 7km is worth digging using a Tunnel Boring machine.
TBM offerings
A Robbins Main Beam TBM is complex in its design, yet relatively simple in concept. The front of the TBM is a rotating cutterhead that matches the diameter of the tunnel. The cutterhead holds disc cutters (ranging from 14″ to 20″ in diameter) which are positioned for optimal boring of the given rock type. As the cutterhead turns, hydraulic propel cylinders push the cutters into the rock. The transfer of this high thrust through the rolling disc cutters creates fractures in the rock, causing chips to break away from the tunnel face. A unique floating gripper system pushes on the sidewalls and is locked in place while the propel cylinders extend, allowing the main beam to advance the TBM.
1. Main beam TBMs
What is a Main Beam TBM?
A Robbins Main Beam TBM is complex in its design, yet relatively simple in concept. The front of the TBM is a rotating cutterhead that matches the diameter of the tunnel. The cutterhead holds disc cutters (ranging from 14″ to 20″ in diameter) which are positioned for optimal boring of the given rock type. As the cutterhead turns, hydraulic propel cylinders push the cutters into the rock. The transfer of this high thrust through the rolling disc cutters creates fractures in the rock, causing chips to break away from the tunnel face. A unique floating gripper system pushes on the sidewalls and is locked in place while the propel cylinders extend, allowing the main beam to advance the TBM.
The machine can be continuously steered while gripper shoes push on the sidewalls to react the machine’s forward thrust. Buckets in the rotating cutterhead scoop up and deposit the muck onto a belt conveyor inside the main beam. The muck is then transferred to the rear of the machine for removal from the tunnel. At the end of a stroke the rear legs of the machine are lowered, and the grippers and propel cylinders are retracted. The retraction of the propel cylinders re-positions the gripper assembly for the next boring cycle. The grippers are extended, the rear legs lifted, and boring begins again
2. Double shield TBM’s
Fractured rock can be an insurmountable obstacle if you buy the wrong machine. Your crew safety and efficiency is at risk, and so is your schedule. With a Robbins Double Shield Tunnel Boring Machine (TBM), your project can have a great safety record and peak performance.
Robbins is no stranger to this type of TBM design. In fact, this is another type of TBM we invented! In 1972 Robbins built the world’s first Double Shield TBM for a customer who anticipated tunneling through large sections of fractured rock. In recent years, several Robbins Double Shield TBMs have broken world records for production.
What is a Double Shield?
A Double Shield TBM consists of a rotating cutterhead mounted to the cutterhead support, followed by three shields: a telescopic shield (a smaller diameter inner shield which slides within the larger outer shield), a gripper shield and a tail shield.
In normal operation (“double shield mode”), the gripper shoes are energized, pushing against the tunnel walls to react the boring forces. The main propel cylinders are then extended to push the cutterhead support and cutterhead forward. The rotating cutterhead cuts the rock. The telescopic shield extends as the machine advances keeping everything in the machine under cover and protected from the ground surrounding it. The gripper shield remains stationary during boring. A segment erector is fixed to the gripper shield allowing pre-cast concrete tunnel lining segments to be erected while the machine is boring. The segments are erected within the safety of the tail shield. It is the Double Shield’s ability to erect the tunnel lining simultaneously with boring that allows it to achieve such high performance rates. The completely enclosed shielded design provides the safe working environment.
If the ground becomes too weak to support the gripper shoe pressure, the machine thrust must be reacted another way. In this situation, the machine can be operated in “single shield mode”. Auxiliary thrust cylinders are located in the gripper shield. In single shield mode they transfer the thrust from the gripper shield to the tunnel lining. Since the thrust is transferred to the tunnel lining, it is not possible to erect the lining simultaneously with boring. In the single shield mode, tunnel boring and tunnel lining erection are sequential operations.
Regardless of the operating mode, working crews remain protected within the shields. Robbins Double Shield TBMs are capable of safely excavating a wide range of geologic conditions on a project. Our Double Shield TBMs are manufactured to suit your project requirements, in diameters from 1.6 m to 15 m (5 to 50 ft).
STANDARD FEATURES ON ALL ROBBINS DOUBLE SHIELD TBMS:
- Flat, low profile cutterhead to enhance face support in broken rock.
- Recessed muck bucket openings with grill bars to prevent ingestion of large rock blocks.
- Back-loading cutters for safe cutter changing in unstable rock conditions.
- Dual thrust-reaction systems, enabling thrust reaction from the tunnel walls or the tunnel lining.
- High-speed segment erector (single- or dual-arm depending on machine diameter) installs pre-cast concrete segments with precision.
- Two-piece articulated telescopic shield offers safety, access to surrounding ground for examination and treatment, and smooth steering through curves.
- Digital guidance system for continuous information on alignment for maintaining strict control of tunnel line and grade.
OPTIONAL FEATURES AVAILABLE ON ROBBINS DOUBLE SHIELD TBMs:
ROBBINS DOUBLE SHIELD TBMs CAN BE CUSTOMIZED WITH:
- Probe drills for pre-excavation investigation and ground consolidation
- Variable cutterhead speed
- Methane and other gas detectors
- Data acquisition system: Automatic acquisition, monitoring and storage of real-time data from the machine functions including penetration rate, thrust pressure, cutterhead speed, gripper pressure and many more machine parameters.
- Automated, precision guidance system, including ring-build option for shielded TBMs
- Guidance data acquisition system
- Closed circuit television systems
- Automatic fire suppression systems
- Closed loop cooling systems for conservation of water
Robbins designs Double Shield TBMs to meet the criteria of each specific project, including the geologic conditions, tunnel design, construction plan, project schedule, site logistics and many other factors. When you contact Robbins, we review your project specifications to determine the best tunneling system for your project. In some cases, an entirely new tunnel boring machine will be the answer and on other projects, the best decision may be to refurbish an existing TBM, to save you time and cost.
3. Tunnel Boring Machines
If the geology of your tunnel ranges from soft soils to weathered rock, then a Robbins Earth Pressure Balance Machine (EPBM) is the correct technical solution for your project. This is particularly true when your project is located in an urban environment and ground surface subsidence cannot be tolerated.
EPBMs are utilized in the construction of rail tunnels, metropolitan subway systems, highway tunnels, and other projects where the tunnel will be constructed either partly or completely in soft soil beneath the water table.
Robbins has integrated over 50 years of TBM design and jobsite experience into our EPBMs. Nobody has a wider range of experience designing innovative machinery to cope with difficult underground conditions. Our engineers will tailor your EPBM to handle the specific challenges of your project. From “Smooth Flow” cutterheads that reduce friction to super-reliable back-filling systems and Variable Frequency Cutterhead Drives, Robbins has taken the traditional EPB design to the next level.
What is an Earth Pressure Balance Machine?
Earth Pressure Balance Machines (EPBMs) are shield machines specially designed for operation in soft ground conditions containing water under pressure. Loose sedimentary deposits with large boulders and a high water table will challenge ordinary TBMs, but not Robbins EPBMs. Robbins EPBMs have an articulated shield that is sealed against the pressure of water inflows up to 10 Bar. Robbins EPBMs control the stability of the tunnel face and subsidence of the ground surface by monitoring and adjusting the pressure inside the cutterhead chamber to achieve a balance with the pressure in front of the cutterhead, hence the name “Earth Pressure Balance.”
The working area inside the EPBM is completely sealed against the fluid pressure of the ground outside the machine.
A screw conveyor removes the fluidized muck behind the cutterhead and in front of the pressure bulkhead. The screw conveyor’s speed and discharge rate is controlled by the operator and is used to control the pressure at the working face and to match the muck discharge rate to the advance rate of the EPBM.
The articulated joint between the forward shield and tail shield is equipped with a high pressure seal that allows angular movement between the shields and prevents water from seeping into the interior of the EPBM.
The EPBM erects the segmented tunnel lining sequentially after each push. Specially designed high pressure seals in the tail shield effectively seal the machine to the outside of the tunnel lining and create a barrier against ground pressure.
When it becomes necessary to enter the cutterhead chamber to inspect the cutterhead or change cutting tools, the workers can safely enter through a manlock while compressed air is used to maintain earth pressure balance to support the working face.
EPBMs can be steered through incredibly small turn radii when necessary by employing the articulation joint and the copy cutter mounted in the cutterhead. Robbins engineers will calculate the correct amount of copy cutter extension and the articulation angle required for the particular radius requirements of a given tunnel.
“The design of the machine, cutterhead, and cutter setup from Robbins shows, after the left line breakthrough at 1,400 m, the wear of the disc cutters was only 4.1 mm, and therefore cutter replacement was unnecessary before it started on the right line tunnel.”
– Li Quan She, Project Manager, CRCC 23rd Bureau, Chengdu Metro Project Line 2
ALL ROBBINS EPBMs ARE EQUIPPED WITH:
- A cutterhead and cutting tools specifically engineered to cope with the expected geology. The cutterhead may be designed with:
- Robbins back-loading disc cutters and drag picks where soil with boulders or massive rock is expected.
- Drag picks only where no rock is expected.
- Full coverage with drag picks and partial coverage with disc cutters where occasional boulders are expected.
- A copy cutter to overcut the tunnel for steering.
- A durable cutterhead with the largest opening capacity in the industry, driven by a proven VFD system.
- A “Smooth Flow” design that reduces cutterhead friction.
- A high capacity main bearing for reliability and longevity.
- High-pressure seals on the cutterhead drive, articulation joint and tail shield to prevent water inflow.
- High-speed rotary segment erector mounted in the tail shield for perfect alignment with the segments.
- Thrust cylinders mounted in the tail shield for correct alignment with the segments.
- Active shield articulation cylinders for steering and transfer of thrust from the tail shield to the forward shield.
- Digital guidance system with continuous display of actual tunnel alignment vs. the design alignment and information for accurately building segment rings.
Robbins designs EPBMs to meet the criteria of each specific project, including the geologic conditions, tunnel design, construction plan, project schedule, site logistics and many other factors. When you contact Robbins, we review your project specifications to determine the best machine for your project. In some cases, an entirely new tunnel boring machine will be the answer. On other projects, the best decision may be to refurbish an existing TBM, to save you time and money.
4. Crossover Machines
For the most difficult projects, Robbins Crossover TBMs can offer time-saving and efficient tunneling. Whether the hybrid design converts between EPB and hard rock modes, between Slurry and hard rock, or between EPB and Slurry is up to you. From heavy duty screw conveyors that handle rock to interchangeable cutting tools, Robbins Crossover TBMs are designed to cross between ground conditions that would typically require multiple machines.
What is a Crossover TBM?
A Crossover TBM (Tunnel Boring Machine) is a specialized type of tunneling equipment designed to handle a variety of geological conditions, including both hard rock and soft ground. The Robbins XRE TBM is a prime example of a Crossover TBM, as it incorporates design elements from both Earth Pressure Balance (EPB) machines and hard rock Single Shield machines.
Key Features of a Crossover TBM:
Versatility: The XRE TBM can efficiently excavate through diverse ground conditions, such as abrasive basalt, watery clays, and mixed geology, making it suitable for projects where the geology may change frequently.
Custom Engineering: Each Crossover TBM is custom-engineered to meet the specific requirements of a project, allowing for optimal performance based on the anticipated ground conditions.
Switching Mechanism: The XRE TBM is equipped with features that enable it to switch between pressurized EPB mode (using a screw conveyor for muck removal) and non-pressurized rock mode (using a belt conveyor) within a few days. This adaptability is crucial for maintaining efficiency when encountering varying ground types.
Interchangeable Cutterhead: The cutterhead of the XRE TBM is designed to allow for interchangeable cutting tools, enabling operators to switch between tungsten carbide bits for soft ground and disc cutters for hard rock.
Advanced Technology: Crossover TBMs come with various advanced features, including high-pressure seals to prevent water inflow, multi-speed gearboxes for navigating challenging ground, and automatic guidance systems for precise tunneling operations.
Field-Proven Performance: Crossover TBMs have been successfully utilized in various challenging environments, demonstrating their ability to lower risks and facilitate difficult excavations when accurate geological information is available.
” Did you know: The Crossover XSE is the most versatile type of TBM? It can be fully customized with both EPB and Slurry TBM features to excavate in nearly all ground conditions.”
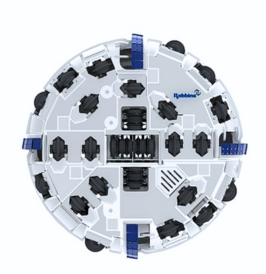
TBM Tunneling
Nepal has been digging tunnels using the conventional drill and blast since 1950s. The D&B method is a standard method to dig tunnels not only in Nepal
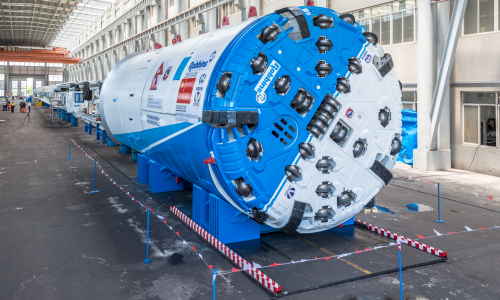
Various Machines
Various Machines include advanced equipment designed for efficient and precise tunneling and excavation.
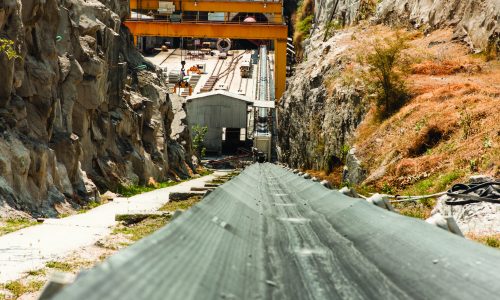
Parts & Services
Parts & Services offer comprehensive solutions for maintaining and optimizing machinery performance in tunneling projects.