Nepal has been digging tunnels using the conventional drill and blast since 1950s. The D&B method is a standard method to dig tunnels not only in Nepal but worldwide. However, in the recent past the use of mechanized tunneling methods using Tunnel Boring Machine (TBMs) are becoming increasingly popular methods to dig tunnels of longer lengths. Nepal used its first TBM in 2015 to dig the tunnel for Bheri Babai Diversion Multipurpose Project. The TBM manufactured by Robbins-A global TBM Company and supplied through MMSM to the contractor appointed by Department of irrigation (DoI), Nepal was successful in completing the tunnel boring of 12.3 KMs of tunnel in just 17 months. This could have taken more than 10 years if dug through Drill & Blast method.
Similarly, the second TBM project in Nepal Sunkoshi Marine Diversion Multipurpose Project under the same department opted to dig its 13.3 KM tunnel using the TBM manufactured and redesigned by Robbins. The tunnel was completed in 19 months about 7 months ahead of schedule.
These successes have proven the worth of TBM’s in Nepal. Now more and more contractors and Developers are exploring the option of using TBMs for their tunnels. The initial capital investment in this method creates a doubt among the tunneler, however it has been seen globally and in Nepal that the significant time saved by using the machine, completely justifies the initial investment. Any tunnels longer than 7km is worth digging using a Tunnel Boring machine.
TBM offerings
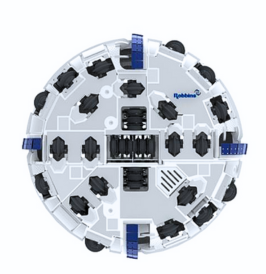
What is a Main Beam TBM?
A Robbins Main Beam TBM is complex in its design, yet relatively simple in concept. The front of the TBM is a rotating cutterhead that matches the diameter of the tunnel. The cutterhead holds disc cutters (ranging from 14″ to 20″ in diameter) which are positioned for optimal boring of the given rock type. As the cutterhead turns, hydraulic propel cylinders push the cutters into the rock. The transfer of this high thrust through the rolling disc cutters creates fractures in the rock, causing chips to break away from the tunnel face. A unique floating gripper system pushes on the sidewalls and is locked in place while the propel cylinders extend, allowing the main beam to advance the TBM.
Project Overview
The Mumbai Water Supply Tunnel runs between the Kapurbawdi and Bhandup areas. The tunnel provides the city’s approximately 20.5 million residents with a reliable water supply, even during the seasonal monsoons that regularly contaminate Mumbai’s water resources. The basalt rock tunnel alleviates Mumbai’s current leakage problems from its aging lines and provide inhabitants with a consistent flow of clean drinking water.
Geology
Abrasive basalt rock and some fractured ground with potential for water inflows.
Onsite First Time Assembly
Onsite First Time Assembly (OFTA) was used to assemble the main bearing, lube system, back-up decks and horizontal, vertical and stacker conveyors. OFTA saved the contractor both time and money by assembling the parts at the jobsite and eliminating pre-assembly at the manufacturing facility in Shanghai, China. The OFTA process took place at the shaft bottom in a 100 m (328 ft) long starter chamber and a 50 m (164 ft) long tail tunnel. TBM components were lowered into the shaft using mobile and gantry cranes.
Excavation and Breakthrough
Due to the urban location of the tunnel, the TBM was launched from a 109 m (357 ft) deep shaft, and its launching sequence included an initial start-up excavation of 50 m (164 ft) with vital back-up decks connected to the TBM using cables. The first bore began March 30, 2012 and upon completion, the decks were lowered and a continuous conveyor system was installed for muck haulage and storage.
Robbins provided both the TBM and conveyor system for the project, as well as Field Service personnel to monitor the equipment and assist with daily upkeep and inspection.
Although the machine was ultimately a success, it did experience its fair share of challenges during the 21-month bore. Difficult ground, including basalt rock, fractured ground, and water inflows, was encountered throughout the tunnel. The tunnel team took all precautionary measures and advanced slowly. The crew maintained good ventilation throughout execution and utilized consistent dewatering to deal with water inflows.
Ground support also played a critical role in poor ground: The rock support system and ring beam erector reduced downtime and stabilized rock. Challenging ground conditions, combined with the sheer depth of the 109 m (357 ft) tunnel, made the machine’s excellent advance rates a particular achievement.
By the end of TBM tunneling, the Robbins machine had reached high rates of 870 m (2,855 ft) per month and 58 m (188 ft) per day, both records for TBM tunneling in India. The contractor stated that the good rates were achieved because of “good performance of the machine and a conveyor system for muck haulage in place of conventional methods.”